Unique VGuard Use Improves Burial Vault Liner Shipping
The Challenge
Indiana Vac-Form, a supplier of burial vault liners, was seeing significant growth. As the business grew, shipping distances increased and logistical challenges like cross docking became unavoidable. The increased mileage and product handling was putting new stress on the corrugated paperboard packaging the company was using. If they were to continue the momentum they were gaining, they were going to need to make some changes.
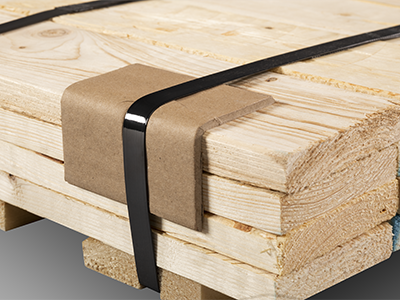
The Bottom Line
Fortunately, they were able to find a solution in VBoard®. Indiana Vac-Form was able to eliminate all their shipping and storing problems and also save on shipping and packing expenses.
How can we help you win?
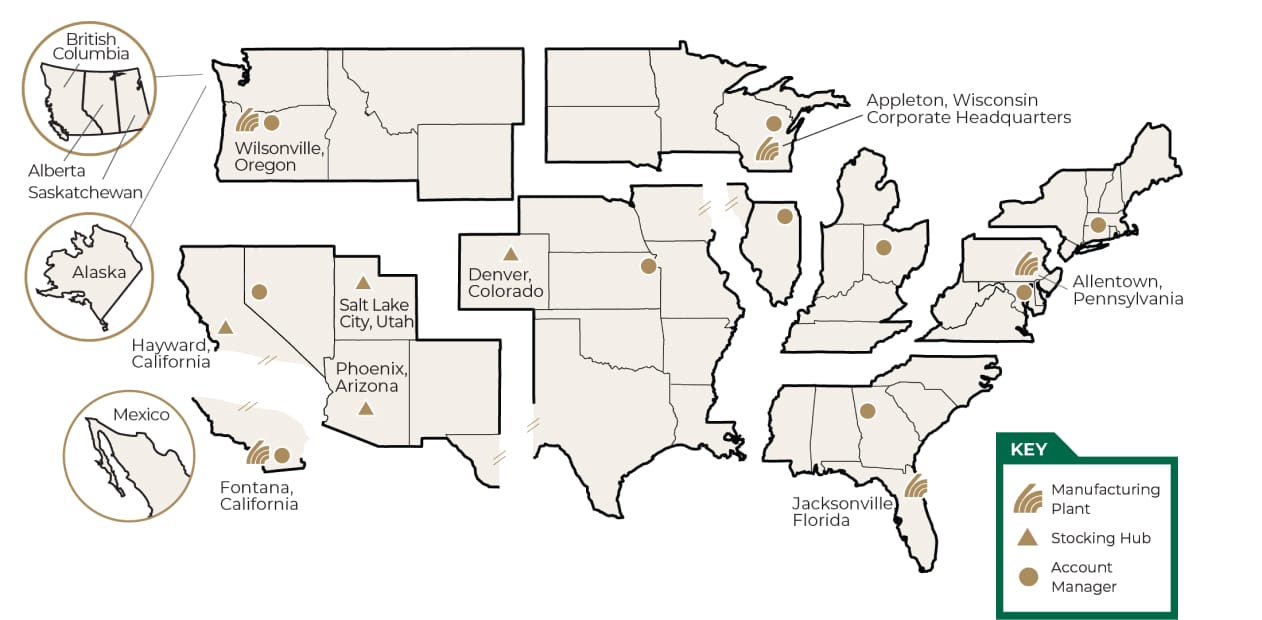