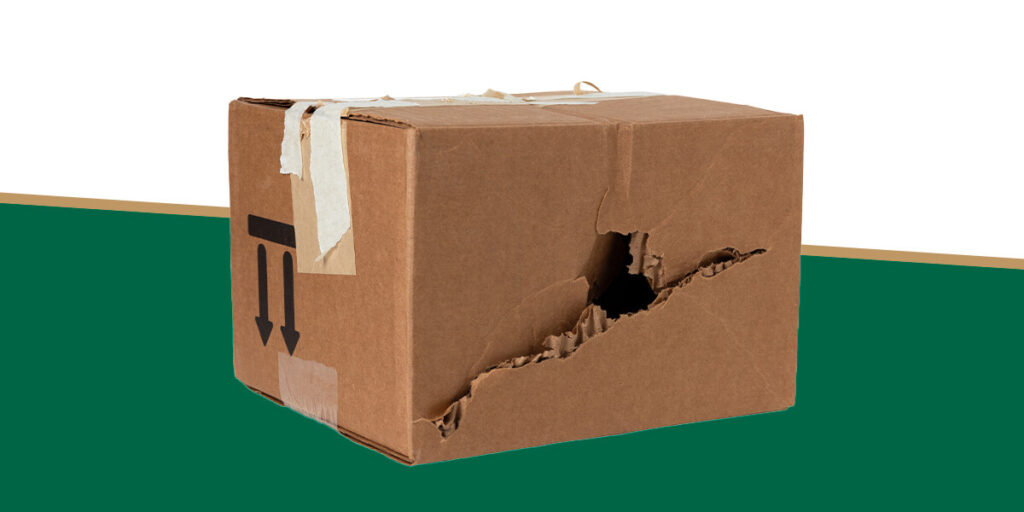
Packaging aims to ensure a package arrives safely and in as good a condition as when a customer would choose one in the store. Unfortunately, among the 161 billion parcels shipped globally yearly, some are more prone to damage during the process. Damaged packages lead to financial loss, delays and disappointment for both the recipient and sender. Preventing damage during shipping is important to avoid unnecessary costs, maintain customer satisfaction and minimize your environmental impact.
For business owners looking for ways to protect packages, let’s show you how to prevent damage during shipping processes.
Understanding Common Causes of Damage
Just under 40% of consumers would avoid ordering from a company again if they received a damaged package. Unlike a physical store where customers can physically inspect items before they buy them, merchants have limited control over how parcels are shipped. However, understanding the two common causes can help them minimize the damages.
Impact During Handling
Even if businesses pack their products themselves, several people sort and carry packages around to deliver them to their destinations. Parcels can also slide around in vehicles carrying cargo. Examples of potential impact points include:
- Corners and edges: These areas are more likely to bear the brunt of impacts and collisions, resulting in chipping, cracking or breaking
- Electronic screens: Devices with screens have sensitive displays that can be easily damaged through cracks and scratches
- Hinges and closures: The shipping process can easily bend, break or misalign moving parts like hinges and closures
- Protruding elements: Items with parts that stick out can easily get bent, broken or snapped off if not properly cushioned in the handling process
- Fragile components: Delicate items or products with fragile attachments can easily snap, bend or detach under pressure or impact
Inadequate Packaging
Inadequate packaging is another common reason for customers receiving damaged items. The following packaging mistakes frequently lead to damages in one way or another:
- Oversized packaging
- Unsuitable packing material for specific products
- Low-cost options involving wasteful production or packaging techniques
- Overpacking products
- Inadequate or difficult-to-open sealing
- Insufficient cushioning in containers
- Lack of protective layers around items
- Uneven weight distribution leading to impact damage
Proper Packaging Techniques
Businesses can reduce damage to their parcels by using the right packaging and protection materials for different products, plus good customer service for returns. Let’s cover some proper packaging techniques.
Selecting the Right Packaging Materials
Choosing a type of packaging material depends on what and how you need to ship. Here are some common packaging materials:
- Glass preserves food and drink flavors while providing a barrier. Although it’s reusable, it can be heavy and easily breakable.
- Plastic is strong, lightweight and flexible. It can be used as packaging or protection like bubble wrap and foam. The downside is that it’s difficult to recycle.
- Paper is lightweight, recyclable and durable in the form of corrugated boxes like paperboard.
- Metal is more durable than glass and plastic, but prone to bending. It’s used to package a diverse range of products.
- Wood can support, protect and transport many types of items and is completely compostable. The downside is that insects and pests can damage wood packaging.
Ensuring a Perfect Fit
When packing products, it’s important to minimize movement within packages. Try these three techniques to secure items in a box:
- Choose a box size that’s only slightly larger than the item you’re shipping
- Use fillers in empty spaces between a product and the box so items remain secure
- Wrap every item with cushioning material, even products that aren’t considered fragile
Reinforcing High-Risk Areas
Another way to protect items from receiving damage during shipment is to identify vulnerable points in the package and strengthen those areas:
- Corners and edges: Corner and edge protection are good for packages containing furniture, appliances, electronics, doors and windows
- Pallets: Top-to-bottom protectors can stabilize and pad stacked pallets and are usually made from wood or lightweight laminated paperboard
- Irregular shapes: Heavy, large or irregular-shaped products often need to be shipped in crates with enough strength for stacking
Labeling and Handling Instructions
Shipping packages can be a complicated and delicate process. Suppose you want to ensure your packages get to their destinations damage-free and with no delays because of shipping regulations. In that case, using clear and accurate labeling and providing handling instructions is important. Here’s a list of labels and handling instructions to consider:
- Fragile: Use more than one fragile sticker on the sides and top of the box so handlers know to handle the parcel with extra care
- This side up: This label ensures the package won’t be accidentally placed upside down
- Non-stackable: This label tells people that other parcels can’t be placed on this package
- Temperature sensitive: Temperature guidelines ensure that perishable goods are delivered in safe condition
- Hazardous: Hazardous goods are considered dangerous when their properties pose any risk to someone’s health and safety, property or the environment. Handling instructions for various hazardous items is necessary for transportation safety and may include explosives, gasses, flammable and combustible items, dangerous when wet products, oxidizing substances and toxic material.
Choosing the Right Shipping Carrier
The final line of defense you can add to protect your packages is to choose the right shipping carrier with experienced employees and weigh your insurance options.
Shipping Carrier Options
The following tips will help your research for shipping carriers:
- Compare carriers in terms of reliability and handling practices
- Find a company with a good reputation by reading customer reviews and feedback
- Look for a carrier that can ship your items to multiple national or international destinations
- Find out if the carrier can ship your type of product, especially if they’re fragile, expensive, perishable or hazardous
Insurance Options
Parcel or shipping damage insurance prevents financial loss incurred by any shipping damages, lost packages or theft. Insurance covers up to the value of the shipped items plus shipping costs. Some carriers automatically include insurance in some of their shipping services. The following are situations in which you should purchase additional insurance:
- If you’re shipping high-value items
- When packages are valued at more than the default coverage
- If you’re shipping internationally
Prevent Damage During Shipping With Great Northern Laminations®
Our protection solutions are unique and limitless. With our protective packaging products, we can solve your industry’s most complex packaging challenges, from protecting the corners and edges of your products to providing extra stacking strength and stabilization for pallets. Our diverse, innovative paperboard protectors are practical and cost-effective while safeguarding your products during handling, storage and shipping.
Contact Laminations to get in touch with a representative and learn about the solutions we can offer for your package shipping needs.